The Role of Processing Aids for Plastics Manufacturers and Mold Makers: A Comprehensive Overview
- Heat Tech Systems
- Mar 18
- 4 min read
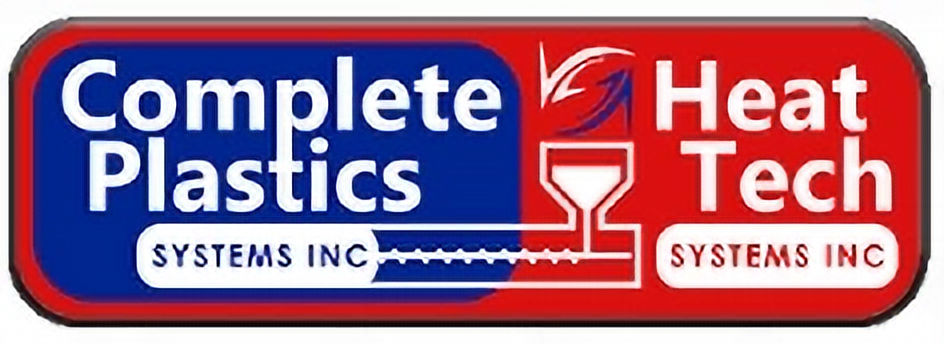
In the fast-paced world of plastics manufacturing and mold making, staying ahead often comes down to efficiency, quality, and consistency. Processing aids are integral in ensuring that production processes run seamlessly. This blog post explores various types of processing aids used in the plastics industry, including mold releases, ejector pin greases, mold cleaners, rust preventatives, MRO (Maintenance, Repair, and Operations) products, and purging compounds. Each of these aids plays a vital role in enhancing the effectiveness and productivity of mold makers and plastics manufacturers.
Understanding Processing Aids for Plastics Manufacturers
Processing aids consist of specialized chemicals added during the manufacturing of plastics. Their primary purpose is to facilitate smoother operations, improve product quality, and minimize production issues. By significantly enhancing the performance of polymers during molding, extrusion, and other processing methods, these aids are critical for both manufacturers and mold makers.
For instance, a study showed that using processing aids can lead to a 20% reduction in defect rates during production. They minimize friction, prevent adhesion, and ensure cleanliness, which ultimately results in a more streamlined and cost-effective manufacturing experience.
Mold Releases
Mold releases are agents that keep plastic products from sticking to mold surfaces during demolding. They create a thin film, making it easier to remove finished parts without damage.
Using mold releases can drastically cut down production delays and costs linked with part removal. For example, companies have experienced a 30% reduction in cycle times by implementing mold releases effectively.
There are several types of mold release agents available, including:
Silicone-based: Often used for their high heat resistance and easy application.
Wax-based: Good for lower temperature applications and sustain mold surface integrity.
Chemically bonded: Ideal for long-term use in high-volume production settings.
The choice of mold release depends on the specific plastic being molded and the mold characteristics. Please visit www.completeplastics.com for more information.
Ejector Pin Greases
Ejector pin greases are crucial for lubricating ejector pins, facilitating their smooth operation during the molding process. Ejector pins are essential components that help eject the molded parts from the mold cavity.
Their use minimizes wear on the pins, extending the lifespan of both the mold and the machinery involved. For example, regular use of the right grease can provide a 40% increase in the lifespan of ejector pins based on laboratory findings.
When selecting the correct grease, consider specific requirements such as temperature stability and compatibility with various plastics. This careful selection ensures optimal performance in the long run.
Mold Cleaners
Maintaining the cleanliness of molds is essential. Over time, residues from mold releases, dust, and plastic remnants can build up on mold surfaces, causing defects in the molding process.
Regular cleaning with specialized chemical agents can help dissolve and remove these residues while preserving mold integrity. Companies that utilize effective mold cleaning solutions report a 25% increase in production efficiency due to fewer defects and delays in the manufacturing process.
It's crucial to select mold cleaners compatible with both the mold material and the type of plastic being processed. Many cleaners are specifically formulated for specific residues and enhance production flow when used appropriately.
Rust Preventatives
Rust preventatives are vital in maintaining metal molds and components in the manufacturing process. Exposure to moisture can lead to corrosion, which significantly affects mold performance and production quality.
Using rust preventatives forms a protective barrier that prevents moisture contact. Companies using effective rust prevention methods have reported up to a 50% reduction in mold maintenance costs thanks to less frequent need for replacements.
Selecting the right rust preventative is key. Some formulations offer long-term benefits, while others are designed for short-term use, making it important to understand the specific needs of your molds.
MRO (Maintenance, Repair, and Operations)
MRO products are essential for the ongoing maintenance and repair of tools and equipment in plastics manufacturing. This category includes lubricants, cleaners, adhesives, and various maintenance tools that keep manufacturing facilities operational.
Adopting good MRO practices is crucial for minimizing downtime. Ensuring that equipment is in good working order can lead to a 15% increase in production capacity, resulting in substantial savings.
Regular audits of MRO practices allow manufacturers to identify which products are most effective and make informed decisions for targeted investments.
Purging Compounds
Purging compounds clean out extruders and molds in plastic processing machinery. They effectively remove residues from previous runs, enabling smoother transitions when switching types of plastic.
Utilizing purging compounds can significantly reduce the time spent cleaning machinery. For example, the proper use of purging compounds can cut cleaning time by about 30%, allowing quicker production changes.
Selecting the right purging compound based on the plastics being processed is crucial. Specific formulations provide varying effectiveness, making customization necessary for optimal results.
Advantages of Using Processing Aids
Using processing aids provides numerous benefits to plastics manufacturers and mold makers. Key advantages include:
Increased Efficiency: By streamlining production and reducing cleaning time, processing aids result in higher output levels. Facilities leveraging these aids can increase production by as much as 20%.
Enhanced Quality: The right processing aids help maintain high product standards, limiting defects and ensuring consistent quality.
Cost Reduction: Reducing wear and scrap rates can lead to significant savings over time. For example, manufacturers can see up to a 30% decrease in operational costs with proper aid usage.
Extended Equipment Life: Regular maintenance with quality processing aids can prolong equipment lifespan and reduce the frequency of necessary repairs.
Faster Turnarounds: Improved cleaning and maintenance practices allow quicker transitions between production runs, helping manufacturers meet customer demands more effectively.
Final Thoughts
In summary, processing aids are essential for plastics manufacturers and mold makers. Products like mold releases, ejector pin greases, mold cleaners, rust preventatives, MRO products, and purging compounds are fundamental in boosting productivity, improving product quality, and cutting operational costs.
Investing in the right processing aids ensures smoother operations and higher production standards. By understanding specific manufacturing needs and selecting the appropriate aids, manufacturers can achieve significant improvements in efficiency and overall effectiveness.
With the ongoing advancement of chemical formulations, processing aids will continue to play a central role in the evolving plastics manufacturing landscape. By carefully applying these essential aids, mold makers and plastics manufacturers can navigate production complexities and achieve remarkable results.
At plasticmoldcleaners.com, we are here to help. Please contact us any time!
Comments