The Ultimate Guide to Efficient Mold Release with DFL Dry Film Lube No. 41112N: A Professional's Secret Weapon
- Heat Tech Systems
- Mar 17
- 4 min read
Efficient mold release is crucial in manufacturing, particularly in injection molding. As companies aim for improved product quality and operational efficiency, the selection of mold release agents becomes vital. Among the many options in the market, DFL Dry Film Lube No. 41112N emerges as a must-have tool, known for its exceptional performance and powerful mold release properties. This guide highlights the features, benefits, and applications of DFL Dry Film Lube, showcasing why it is essential for modern plastics manufacturing.
Understanding DFL Dry Film Lube Mold Release No. 41112N
DFL Dry Film Lube No. 41112N is a premium mold release agent crafted specifically for injection molding processes. It excels in environments that demand clarity, deep draws, and minimal traction, all crucial for yielding flawless molded parts.
Manufacturers enjoy swift production runs thanks to DFL's fast-drying formulation. Unlike traditional wet-release agents, which can slow down operations and diminish quality, DFL offers a quick-drying solution, fitting perfectly into high-demand environments. In fact, facilities using DFL report up to 30% reduction in cycle time, allowing for more parts produced per hour.
Key Features of DFL Dry Film Lube
Fast-Drying: This agent dries quickly, significantly reducing the time molds need to be idle. Users can return to work in just 10 minutes after application.
Compatibility with Hard Resins: DFL works seamlessly with tough materials, such as polycarbonate and nylon. This compatibility prevents damage during the demolding process, a common issue in manufacturing that can lead to costs upward of $10,000 annually due to defects.
Inert Formulation: DFL's unique composition prevents dust and dirt from clinging, ensuring that the final products maintain high quality over time.
Corrosion Resistance: Its ability to withstand harsh environments adds reliability across various industrial applications, leading to longer equipment lifespan and fewer replacements.
Why Choose DFL Dry Film Lube?
Choosing the right mold release agent can have a profound influence on production quality and efficiency. Here are reasons to consider DFL Dry Film Lube No. 41112N:
Enhanced Production Speed: Fast-drying properties lead to quicker turnaround times. Facilities report producing 15-20% more parts per day since switching to DFL.
Improved Surface Finish: Users often notice a superior finish quality, as DFL prevents markings or residues left by other agents. This means less need for reworking, saving time and labor.
Versatility Across Industries: DFL is utilized for a wide range of applications, including automotive parts, household items, and electronic components, making it a versatile choice for diverse workshops.
Applications of DFL Dry Film Lube No. 41112N
Identifying key applications that benefit from DFL Dry Film Lube can enhance its effectiveness in your operations. Below are some areas where its application is particularly advantageous:
1. Injection Molding of Hard Plastics
In the world of manufacturing, hard plastics like polycarbonate and nylon are commonly used. DFL Dry Film Lube simplifies the release from molds, minimizing defects and increasing productivity rates by about 40% according to user reviews.
2. Complex Part Design
Manufacturing intricate parts can present challenges for mold releases. Thanks to DFL's advanced non-traction properties, intricate designs can be effortlessly removed from their molds, ensuring product integrity and quality.
3. Low-Volume Production Runs
For projects that don't require large batch sizes, DFL's quick-drying capabilities become invaluable. Manufacturers can change setups quickly, ensuring that timeline pressures are met without compromising quality.
Advantages of DFL Dry Film Lube No. 41112N
A Cost-Effective Solution
While DFL may have a higher initial cost, the efficiency and quality improvements it offers translate to substantial cost savings over time. Decreased cycle times, lower scrap rates, and better product quality can lead to savings of over 15% on average.
User-Friendly Application
DFL Dry Film Lube is easy to apply, allowing for simple integration into existing workflows. This ease of use minimizes the time needed for training and helps teams achieve results rapidly.
Enhanced Product Quality
Manufacturers using DFL can expect consistent product quality. With its ability to yield smooth surfaces without additional finishing work, customer satisfaction increases, and the chance of rework decreases.
Comprehensive Support
Opting for DFL Dry Film Lube includes access to technical support and best practice advice. This assistance can prove invaluable when making the transition to a new product. At plasticmoldcleaners.com we are here to help with any questions.
Embracing Innovation in Mold Release
DFL Dry Film Lube No. 41112N represents a modern advancement in mold release technology. It delivers unmatched efficiency, quality, and versatility for manufacturing operations. Its swift drying, compatibility with tough resins, and inert properties make it a standout choice for injection molding applications.
By strategically implementing DFL Dry Film Lube into your production processes, you can improve quality and speed. With a focus on enhanced production rates and better surface finishes, this mold release agent is truly an invaluable resource for professionals.
Incorporating DFL Dry Film Lube into your operations can lead to a more efficient and quality-focused approach. With the ongoing demand for excellence in manufacturing, investing in this agent will ensure you remain competitive in an ever-evolving market.
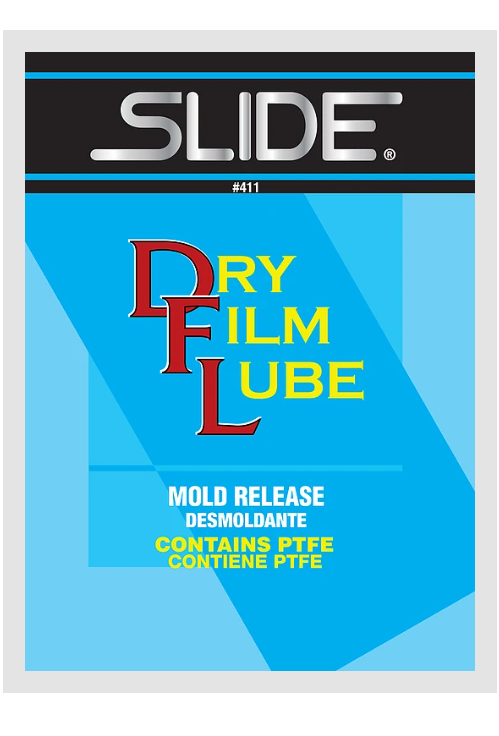
Comments